球阀被广泛的应用在石油炼制、长输管线、化工、造纸、制药、水利、电力、市政、钢铁等行业,流体阻力小,全通径的球阀基本没有流阻,紧密可靠,但球阀的启闭扭矩是反映球阀性能的关键参数之一,它是指阀门开启或关闭所必须施加的作用力或力矩,是阀门在介质压力作用下动作的一项综合技术指标。随着时代发展,进入21世经以后,生产和制造技术有了显著优化提高,为了解决球阀减轻启闭力矩,降低成本,滚动轴承在球阀中得到应用,使其启闭扭矩明显降低,延长使用寿命,操作性能显著提高。
1 结构设计
在输送矿浆用球阀、水煤浆工况用球阀等大口径固定球阀,阀杆采用防尘和防喷出设计,在结构上确保阀杆只承受阀门启闭力矩,介质的推力由上、下支承轴承担,使阀杆的受力情况有了很好改善,保证阀杆能够长期可靠地工作,上下支承轴均设置有滚动轴承和滑动轴承,由此降低阀门的操作力矩。如图1、图2所示。小径口浮动球阀,阀杆轴颈处设计滚动轴承与密封圈。如图3所示。

图1 固定球阀上承轴结构
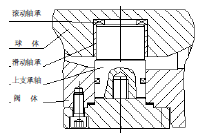
图2 固定球阀下承轴结构
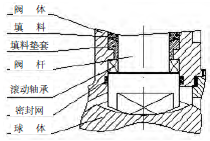
图3 浮动球阀阀杆轴颈结构
2 球阀的摩擦力矩分析
球阀的转矩计算是确定驱动装置的功率及主要零件强度计算的基础。转矩大小决于摩擦力矩和介质流经阀门所产生的动水力矩。动水力矩是由于转轴两动水作用力不等而引起的力矩,是在启闭件脱离阀座密封圈封面后,在介质流动中产生的。它和密封面间的摩擦力矩不会同时产生,在数值上一般小于密封面的摩擦力矩。摩擦力矩一般包括:启闭件与阀座密封面之间的摩擦力矩,阀杆与填料间摩擦转矩,阀杆与轴承之间的摩擦力矩等。如图4所示。
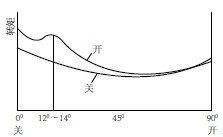
图4 球阀转矩与开度关系
由图4可以看出在球体开启的瞬间,转矩具有最大值。因为这时密封副受到的密封力最大(要承受最大压差及预紧力作用)。随着开度增大转矩逐渐下降,虽然在12°~14°时又略有升高,但总的来说,最大转矩发生在开启瞬间。因此,计算分析阀杆力矩时,按最大压差(即处于全关状态下)进行。在这一阶段,只有摩擦力矩而无动水力矩。如图5所示。

图5 密封面上任意受力分析
设密封面上任一点A的坐标为A(x,y,z),转轴L(即z轴)的方程为
(1)
A点到L距离为
(2)
由几何关系分析,摩擦力的方向是沿A点处绕轴旋转的切向方向并与旋转度方向相反,则摩擦力为
(3)
摩擦力矩为
(4)
摩擦总力矩为
(5)
3 阀杆力矩计算
阀门在石油、化工、电力、城建和工业企业的给排水、供热及供气系统中有着广泛的应用。存些系统中使用的球阀通常处于常开或常闭状态,当一个长期处于关闭状态的球阀需要开启时,关闭与开启的力矩最很大。
固定球球阀的阀杆力矩计算公式:
MF=MQG+MFT+MZC (6)
固定球球阀的球体与阀座密封面间的摩擦力矩计算公式:
MQG=MQG1+MQG2 (7)
由阀座对球体的预紧力产生的摩擦力矩计算公式:
(8)
由介质工作压力产生的摩擦力矩计算公式:
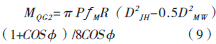
浮动球球阀阀杆力矩计算公式:
MQF=MQF+MFT+MZC (10)
浮动球球阀的球体与阀座密封面间的摩擦力矩计算公式:
MQF=MQF1+MQF2 (11)
进口端阀座密封面与球体间的摩擦力矩计算公式:
MQF1=M'QF1+M''QF1 (12)
进口端阀座对球体预紧力产生的摩擦力矩计算公式:

介质对进口阀座的作用力而产生的摩擦力矩计算公式:

球体与出口阀座密封面间的摩擦力矩计算公式:

填料与阀杆间摩擦力矩计算公式:
(16)
轴承产生的摩擦力矩计算公式:
(17)
式中 MF——球阀的阀杆力矩,N.mm;
MQG——固定球球阀的球体与阀座密封面间的摩擦力矩,N.mm;
MQG1——由阀座对球体的预紧力产生的摩擦力矩,N.mm;
MQG2——由介质工作压力产生的摩擦力矩,N.mm;
MQF1——进口端阀座密封面对球体预紧力产生的摩擦力矩,N.mm;
M'QF1——进口端阀座对球体预紧力产生的摩擦力矩,N.mm;
M''QF1——介质对进口阀座的作用力而产后的摩擦力矩,N.mm;
MQF2——球体与出口阀座密封面间的摩擦力矩,N.mm;
MFT——填料与阀杆间摩擦力
MZC——轴承产生的摩擦力矩,N.mm;
DMW——阀座密封圈与球体接融面外径,mm;
DMN——阀座密封圈与球体接融面内径,mm;
DJH——活动阀座外径,mm;
dQJ——轴颈,mm;
R——球体半径,mm;
Φ——球体与密封圈与球体接融面内径,(°);
qM——球体最小预紧比压,MPa
P——设计压力,MPa
fM——球体与密封面间摩擦因数(对聚四氟乙烯密封面fM=0.05,对卡普隆密封面fM=0.1~0.15,对钢密封面fM=0.3)
fZ——轴承摩擦因数(用聚四氟乙烯制的滑动轴承为0.05~0.1,滚动轴承为0.002,钢与钢0.30,钢与青铜为0.20)
假设DN200-1.6MPa,活动阀座外径DJH为240mm,轴颈为50mm;DN50-1.6MPa,活动阀座外径DJH为68mm,轴颈为25mm;从上面公式(17)可以得出,DN200-1.6MPa用滚动轴承可以减轻阀杆力矩539N.m;DN50-1.6MPa用滚动轴承可以减轻阀杆力矩27N.m。
4 滚动轴承受力分析
滚动轴承在工作中,在通过轴心线的轴向载荷(中心轴向载荷)Fa作用下,可认为各滚动体平均分担载荷,即各滚动体受力相等。当轴承在纯径向载荷Fr作用,下如图6所示,内圈沿Fr方向移动一距离δ0,上半圈滚动体不承载,下半圈各滚动体由于个接触点上的弹性变形量不同承受不同的载荷,处于Fr作用线最下位置的滚动体承载最大,其值近似为5Fr/Z(点接触轴承)或4.6Fr/Z(线接触轴承),Z为轴承滚动体总数,远离作用线的各滚动体承载逐渐减小。对于内外圈相对转动的滚动轴承,滚动体的位置是不断变化的,因此,每个滚动体所受的径向载荷是变载荷。

图6 滚动轴承径向载荷的分析图
5 当量动载荷计算
轴承的基本额定动载荷是在假定的运转条件下确定的。基中载荷条件是:向心轴承仅承受径向载荷,推力轴承仅承受纯轴向载荷。实际上,轴承在大多数应用场合,常常同时承受径向载荷和轴向载荷,因此,在进行轴承计算时,必须把实际载荷转换与确定额定动载荷条件相一致的当量动载荷。当量动载荷的一般计算公式为:
P=XFr+YFa (18)
式中
P——当量动载荷,N;
Fr——径向载荷,N;
Fa——轴向载荷,N;
X——径向动载荷系数;
Y——轴向动载荷系数。
6 额定静载荷计算
对低速旋转或缓慢摆动的轴承,应分别计算额定动载荷和额定静载荷。取其中较大者选择轴承。额定静载荷的计算公式为:
(19)
式中 C0——基本额定静载荷计算值,N;
P0——当量静载荷,N;
S0——安全因数,静止轴承和缓慢摆动或转速极低的轴承S0见表1;
C0r——轴承尺寸及性能表中所列径向基本额定静载荷,N;
C0a——轴承尺寸及性能表中所列轴向基本额定静载荷,N。
当量静载荷计算公式:
a=0的向心滚子轴承,径向当量静载荷P0r=Fr;
向心球轴承和a≠0的向心滚子轴承,径向当量静载荷

(X0为径向静载荷系数,Y0为轴向静载荷系数);
a=90°的推力轴承,轴向当量静载荷P0a=Fa;
a≠90°的推力轴承,轴向当量静载荷P0a=2.3Frtanα+Fa;
7 滚动轴承的摩擦力矩算
滚动轴承主要有:滚动体与滚道之间的滚动摩擦和滑动摩擦;保持架与滚动体及套圈引导面之间的滑动摩擦等。其大小取决于轴承的类型、尺寸、载荷、转速等。轴承的摩擦力矩一般计算公式为:
M=μFd/2 (20)
式中
M——轴承摩擦力矩,N.mm;
μ——轴承摩擦因数;(滚针轴承-满针μ为0.0025~0.0040;滚针轴承-有保持架μ为0.0020~0.0040;单向推力球轴承μ为0.0013~0.0020;角接触球轴承μ为0.0018~0.0025)
F——轴承载荷,N,
d——轴承内径,mm。
8 需要的最小轴向载荷计算
在滚动轴承在运转中滚动体受离心力矩作用,滚动体和滚道之间产生相对滑动,导致轴、座圈分离,为保证承正常工作,必须施加一定的轴向载荷预紧。所需的最小轴向载荷公式为:
对推力球轴承:
(21)
对推力圆柱滚子轴承、推力圆锥滚子轴承:
(22)
对于推力调心滚子轴承:
(23)
对于推力滚针轴承:
(24)
式中
Famin——需要的最小轴向载荷,kN;
Fr——径向载荷,kN;
C0a——基本额定静载荷,kN;
A——最小载荷常数;
n——转速,r/min。
9 滚动轴承材料选择
滚动轴承材料必须具有的特性:接触疲劳强度高、硬度高、纯洁度高、耐磨性好、组织稳定性好、机械加工性能好。材料的选择,设计人员依据球阀使用工况和环境下工作要求而定,如表1所示。
表1 常用滚动轴承常用材料


10 滚动轴承装配注意事项
滚动轴承在球阀很重要,通过多年球阀装配实践,提出了滚动轴承装配的方法和要点,按要点装配可有效的提高轴承装配质理,从而保证滚动轴承在球阀中起到的作用,总结出如下轴承装配方法。
1)装配前检查项目及要求
利用千分尺、内径量表核对轴孔及轴承尺寸是否符合要求,0-260mm内径轴承的过盈量0.01-0.03mm;加热前,仔细检查轴承外观是否有损伤、裂纹,保持架完整、无缺陷;装配前必须清理和清洗干净,不得有毛刺、飞边、氧化皮、锈蚀、切屑、油污、着色剂和灰尘等。
2)装配过程中的注意事项
轴承采用机油和轴承加热器加热进行热装,温度不得超过100℃;需用锤击轴承时,应垫紫铜棒、铝棒等;采用润滑脂的轴承,装配后应注入相当于轴承空腔容积约50%的符合规定的清洁润滑脂,凡稀油润滑的轴承,不准加润滑脂;可拆卸轴承时,必须严格按原组装位置,不得装反或与别的轴承混装,可调头装的轴承,装配时应将轴承的标记端朝外。
3)装配后检查项目及标准
在同轴的两个轴承中,必须有一个可以随轴热膨胀时产生轴向移动,热膨胀间隙ΔL,一般不大于0.5mm;滚动轴承装好后,用手转动应灵活;轴承内圈应紧靠轴向定位端面,其允许最大间隙,对圆锥滚子轴承和角接触轴承为0.05mm,其他轴承为0.1mm。
11 预测的不确定性
不管按什么设计方法,实际轴承能否达到计算的性能,常常不能断定,这主要是因为根据尺寸对扭矩能否减少的影响来判断时,就会发现由于实际制造公差使尺寸变化非常大。运转中滚动轴承可能由于装配不当、润滑不良、水分和异物侵入、腐蚀、过热、和过载等原因造成过早其损坏;即使在安装、润滑和使用维护都正常的情况下,经过一段时间的运转,轴承也会出现疲劳剥落和磨损。滚动轴承虽然结构简单,但失效形式却表现在多样性,主要的失效形式有:
1)疲劳失效
疲劳是滚动轴承失效的主要形式,常表现为滚动体或内外圈滚道表面脱落或蜕皮,初期是在接触表面形成不规则凹坑,而后逐渐延伸成片,冲击载荷造成振动和噪声的加剧,交变的疲劳应力是造成疲劳剥落的主要原因,有时也与润滑不良或强迫安装有关,而通常所说的轴承寿命即是指轴承的疲劳寿命。
2)磨损失效
磨损是滚动轴承失效的另一常见形式,是轴承滚道、滚动体、保持架、座孔或轴颈由于机械原因引起的表面磨损。磨损造成轴承游隙增大、表面粗糙度增加,轴承运转精度降低、振动和噪声增大。磨粒(尘埃、导物的侵入)及润滑不良造成磨损的根本原因。
3)腐蚀失效
润滑油、水份或湿气产生的化学腐蚀,电流通过引起电火花而产生的电腐蚀及轴承内外圈与座孔或轴颈存在微小相对运动形成微振腐蚀是滚动轴承腐蚀失效的三种表现形式,表面腐蚀导致高精度轴承精度一丧失而失去其功能。
4)断裂失效
滚动轴承零件材料有缺陷和热处理不良,运行中过载、转速过高、润滑不良或装配不善造成过大的热应力等可能引起轴承零件轴承出现裂纹或断裂、加速其劣化。
12 总结
上述的结构经长期适用运行证明,滚动轴承在球阀应用,阀门操作力矩小。不管固定球阀,还是浮动球阀都要防尘结构设计,防止细小颗粒进入滚动轴承,避免滚动轴承卡死失效;根据球阀适用工况正确选用滚动轴承的材料,不同介质温度、耐腐选用滚动轴承材料不同,轴承材料选择恰当直接关系到能否满足机构的功能与使用要求,对轴承工作性能和疲劳寿命具有决定性的影响。