1 概述
随着石油、化工和燃气行业的迅速发展,尤其是液化天然气(LNG)作为一种新兴能源的广泛应用,使得LNG用超低温阀门的需求量迅速增加。由于LNG常压下的温度为-162℃,且易燃易爆,因此对LNG超低温阀门的密封性能的要求比普通阀门严格。常温下工作的蝶阀采用金属-非金属密封副即能实现良好的密封,是由于常温下非金属材料的弹性大,密封所需的比压小。但是,由于非金属材料的膨胀系数较金属材料大得多,使得其低温时的收缩量与金属密封件、阀体等配合件的收缩量相差较大,从而导致密封比压严重降低而使密封性能大大下降。另外,由于大多数非金属材料在深冷温度下会变硬和变脆而失去韧性,从而导致应力松弛。因此目前在设计工作温度低于-70℃的低温阀门时,通常采用金属-金属密封副。但在低温条件下,金属材料的强度和硬度提高,塑性和韧性降低,导致低温冷脆现象的发生,严重影响到阀门的性能和安全。本文提出了一种具有金属-非金属密封副的高密封性能双偏心超低温蝶阀,并采用ANSYS有限元分析软件对其密封副进行低温下结构应力分析,优化密封结构参数。
2 结构特性
LNG超低温蝶阀(图1)的公称通径为150mm,公称压力为150LB(1.0MPa)。密封副由阀体、蝶板、阀杆以及设置于阀体内的密封圈、弹簧圈、预紧环、支撑环、挡圈及挡销等组成(图2)。
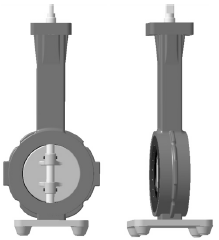
图1 超低温蝶阀的三维模型
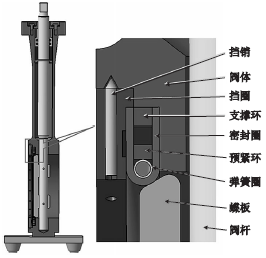
图2 超低温蝶阀的密封副结构
阀体与蝶板通过阀杆连接到一起,阀体与阀杆之间采用间隙配合,阀杆可在阀体内转动。阀杆与蝶板上的两个凸起的内孔采用过盈配合,并用销钉将其固定,以防止两者相对转动。密封圈的截面为U形,弹簧圈套在密封圈的U形槽内,并与其根部紧密接触,可使密封圈在弹簧圈的弹力作用下沿径向收缩,保证密封的可靠性,并能保证密封圈磨损后也能在弹力作用下具有很好的密封性。另外,为防止密封圈在超低温条件下变硬变脆,采用耐低温的聚三氟氯乙烯密封材料来保证密封的高可靠性。弹簧圈的外径处由预紧环套住,预紧环采用奥氏体相变终了温度Af较高的高温镍钛基形状记忆合金材料制成,加工时先在奥氏体状态下将其加工到一定直径,然后在深冷条件下(低于Mf点)进行扩径变形,使其内径略小于弹簧圈的外径,这样装配时可使弹簧圈产生一定的预变形,增大弹簧圈的弹力,进而提高密封圈的密封压力,保证密封的可靠性。为保证密封圈的安装刚度,在其内的U形槽内还装有支撑环。密封圈、预紧环和支撑环装入密封圈后由挡圈压装于阀体内部的凹槽内,并通过挡销固装在阀体上。
3 密封副的设计计算
蝶板密封关闭时的计算密封比压q为
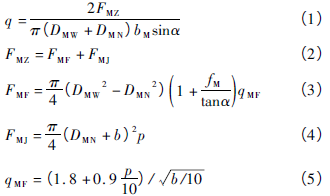
式中q———计算密封比压,MPa
DMW———密封面外径,mm
DMN———密封面内径,mm
b———阀座密封面宽度,mm
α———蝶板密封面与密封圈弧面接触半角,(°)
FMZ———密封面上的总作用力,N
FMF———密封面上的密封力,N
FMJ———密封面上的介质作用力,N
p———设计压力,MPa
fF———密封面摩擦因数
qMF———密封必需比压,MPa
若使阀门能够达到密封要求,必须满足qMF<q<[q]([q]为密封许用比压,MPa)。
由计算可知,阀座密封面宽度b越大,密封必需比压qMF和计算密封比压q就越小,越容易满足密封许用比压[q]。
4 密封副的有限元分析
4.1 有限元模型
由于蝶阀密封副是轴对称的,因此可以把密封副的研究由三维问题变为二维问题。为简化分析,只取密封副部分(图3)。由于挡圈、密封圈、支撑环、预紧环和弹簧圈都是紧固在阀座上,相互之间的作用力较小,因此将这些零件进行粘合处理,不考虑零件之间的接触问题。分析采用二维实体单元PLANE182,整个模型中共有1024个单元,148840个节点。为了应力应变分析,对密封圈与蝶板接触部分的边界节点进行相应的编号(图4)。
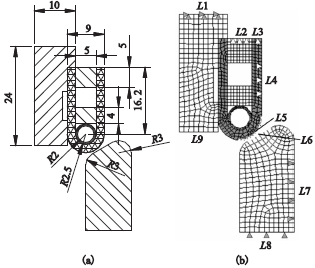
(a)数学模型(b)有限元模型
图3 密封副在密封前状态下的简化模型
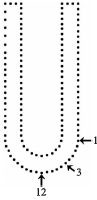
图4 密封圈节点标号
4.2 材料模型
整个分析模型由三种材料构成,其中弹簧圈材料为Inconel718镍基合金,密封圈材料为聚三氟氯乙烯(PCTFE),其他材料均为316L不锈钢。
表1 材料性能参数(-196℃)
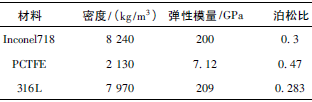
4.3 接触对定义
密封圈与蝶板是密封副的主要工作部位,因此需对两者进行接触分析,即在它们之间定义接触对。在定义刚-柔体的面-面接触对时,应将刚性面定义为“目标”面,柔性面定义为“接触”面,因此本模型中将蝶板的接触面设为“目标”面,选用TARGE169单元,将密封圈的接触面设为“接触”面,选用CONTA175单元(图3(b)所示,边界L5、L6即为接触对,其中L6为目标面,L5为接触面)。
4.4 初始边界条件及加载
由于挡圈的边界L1受阀体和固定销的限制,在两个方向上都不能移动,故对其进行全约束,即UX=0、UY=0,保证其位置固定不变。
支撑环的边界L2和密封圈的边界L3在Y方向上受阀体的限制,故对边界L2和L3进行UY=0的约束,限制其在Y方向的移动;密封圈的边界L4在X方向上受阀体的限制,故对其进行UX=0的约束,限制其在X方向的移动;蝶板在Y方向上受阀杆的限制,故对其边界L8进行UY=0的约束,限制其在Y方向的移动。
由于阀座密封面宽度b对密封副的密封性能有着显著的影响,因此通过对蝶板设置不同的位移实现不同密封面宽度条件下的密封副有限元模拟。模拟的密封面宽度分别为2mm、4mm和6mm,对应的蝶板位移分别设为1mm、2mm和3.3mm。对蝶板边界L7分别施加X方向的约束,即UY=-1mm、UY=-2mm和UY=-3.3mm。另外,还要在蝶板的边界L7上施加P=1.0MPa的工作压力。
4.5 模拟结果及分析
由密封副在不同阀座密封宽度时的等效应力分布(图5)分析可知,整个密封副中弹簧圈所受等效应力最大,其次是密封圈与蝶板的密封面处。随着阀座密封宽度的增大,密封副内的等效应力明显增大,造成密封比压也随之增大,使得弹簧圈在阀座密封宽度b=4mm时开始发生明显的畸变。
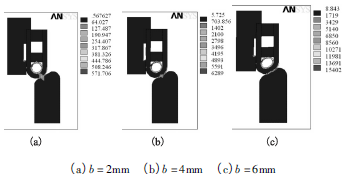
图5 密封副在不同阀座密封面宽度时的等效应力分布
由密封副在不同阀座密封宽度时的剪切应力分布(图6)分析可知,剪切应力的最大值出现在弹簧圈的下半部分,且剪切应力值也随着阀座密封宽度的增大而增大。另外,在阀座密封面的法向方向上,挡圈、弹簧圈、密封圈和蝶板的剪切应力均较自身的其他部分明显增大。
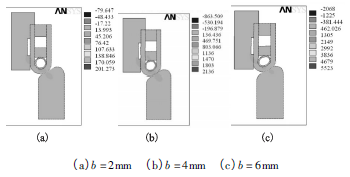
图6 密封副在不同阀座密封面宽度时的剪切应力分
由密封副在不同阀座密封宽度时的等效应变分布(图7)分析可知,当密封宽度为2mm时,密封圈发生了明显的变形,而弹簧圈几乎没有变形,这是因为弹簧圈的弹性模量远远大于密封圈的弹性模量,虽然其所受应力比密封圈大得多,但还不足以使其发生较大的变形。随着密封宽度的增大,密封圈的变形区域逐渐增大,使密封比压也明显增大,迫使弹簧圈也随之发生了变形。
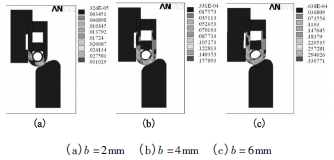
图7 密封副在不同阀座密封面宽度时的等效应变分布
由密封副在不同阀座密封宽度时的剪切应变分布(图8)分析可知,与剪切应力的分布相似,各零件的剪切应变也是在密封面的法向方向上相对较大,且随着阀座密封宽度的增大,剪切应变逐渐增大。各零件中,密封圈的剪切应变最大,这是因其与蝶板直接作用,且弹性模量最小造成的。
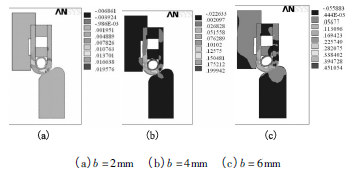
图8 密封副在不同阀座密封面宽度时的剪切应变分布
由不同阀座密封面宽度时密封面上的等效应力分布(图9(a))分析可知,密封面上的等效应力最大值发生在接触面的节点上,随着阀座密封面宽度的增大,密封面上的等效应力逐渐增大,并使密封圈远离密封面一侧的等效应力也逐渐增大,这是密封比压增大造成弹簧圈变形并作用于该处的结果。
由不同阀座密封面宽度时密封面上的剪切应力分布(图9(b))分析可知,由于简化为二维模型,剪切应力只表示密封圈在XY面受的剪切作用。图中负值表示剪切应力值与XY平面的正方向相反。由于剪切作用容易使密封圈发生撕裂,因此剪切应力最大值处是密封圈最易撕裂处,在密封副设计时应保证该处的剪切应力小于密封材料的撕裂强度。

(a)等效应力 (b)剪切应力
图9 不同阀座密封面宽度时密封面上的应力分布
从不同阀座密封宽度时密封面上的接触应力分布分析(图10),当阀座密封面宽度为2mm和4mm时,密封面的接触应力最大值均小于工作压力,因此难以保证密封的安全性。当阀座密封面宽度为6mm时,密封面的接触应力最大值超过了工作压力,能够满足密封要求。因此,在设计该阀门时应使阀座密封宽度b≥6mm才能保证有效密封。
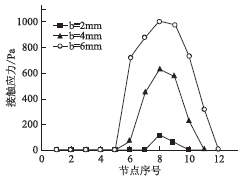
图10 不同阀座密封宽度时密封面上的接触应力分布
由不同阀座密封宽度时密封面上的摩擦应力分布(图11)分析可知,摩擦应力在一定程度上会影响密封件的寿命。在工作状态下,由于密封件长期难以恢复原状,在较大的摩擦力条件下,会使其内部长时间保持较大的应力,这将加速密封件的老化,从而缩短其使用寿命。反之,摩擦应力小,则可延长使用寿命。由图11可以看出,密封面上的摩擦应力是随着密封面的宽度增大而增大的,因此,设计阀门时,在保证密封面宽度满足密封要求的同时,还应采取其他措施减小摩擦应力,以延长密封圈的使用寿命。
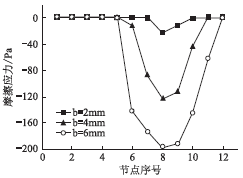
图11 不同阀座密封宽度时密封面上的摩擦应力分布
5 结语
阀座密封宽度对密封副的结构应力和密封性能均有很大的影响。随着密封宽度的增大,密封副所受的应力和应变均增大,密封面所受的等效应力和接触应力也增大,使密封性能提高,但随之也导致了密封面上摩擦应力的增大,使密封圈的使用寿命缩短,因此,还应采取措施减小摩擦应力,延长密封圈的使用寿命。